Products Connectivity & MES
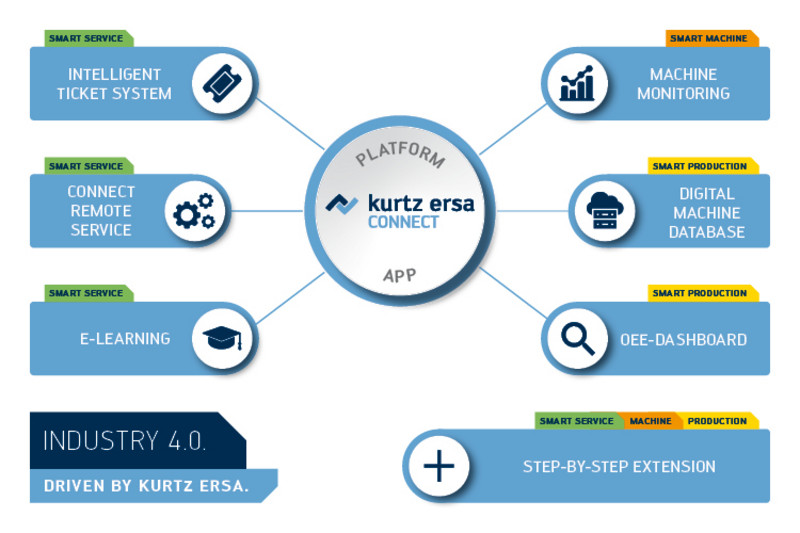
Technological sustainability
on customer side
Modern communication and information technologies connect people and machines. Digitization and networking of the smallest components up to highly complex systems lead to significantly increased productivity. Ersa developers use Industrie 4.0 as a powerful tool to significantly increase processes and technological sustainability on the customer side.
Industry 4.0 is used as a tool to further improve existing processes in the following areas
processes in the following areas:
- Smart Services: Increase in service quality
- Smart Machine: improvement of the process quality of Ersa equipment
- Smart Production: 100% transparency in the production process
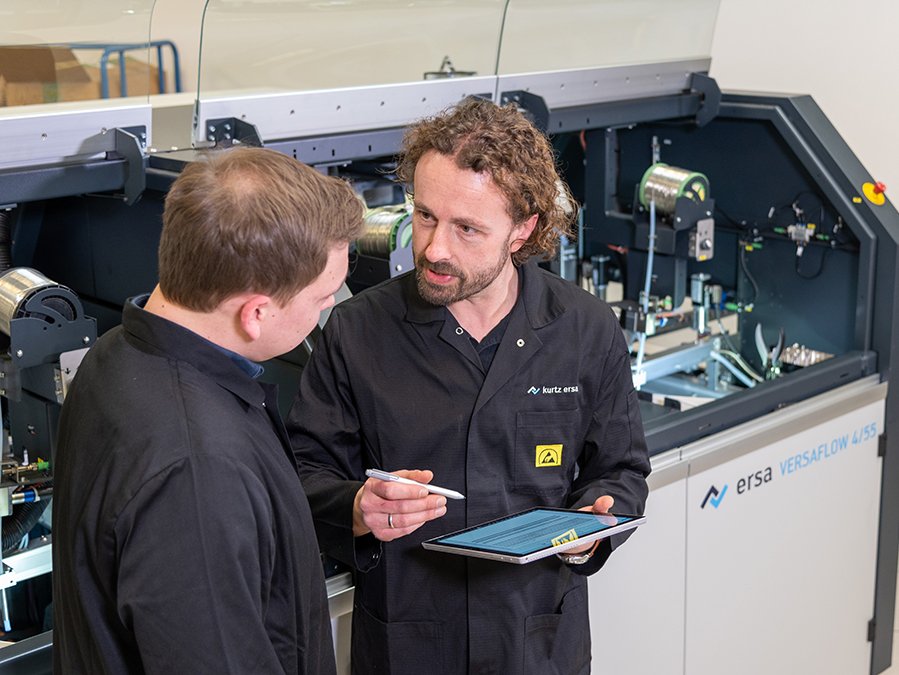
Further optimize processes
Take the next step towards digital production with us and make your VERSAFLOW 4 fit for the future. Industry 4.0 is the instrument to further improve existing processes in the areas of Smart Service, Smart Machine and Smart Production.
With the Kurtz Ersa CONNECT platform, we offer an end-to-end hardware and software infrastructure ranging from the machine portfolio to standardized interfaces to customer systems. Kurtz Ersa´s digital offerings are accessible regardless of location and device and increase the reliability and availability of each individual plant. Where once there was a situational reaction, information can now be evaluated and interpreted in advance based on data.
Industry 4.0 at Kurtz Ersa at a glance
Your Values
- Increasing service speed/quality and process reliability
- Obtaining important data for process and machine monitoring
- Benefit from digital solution concepts
- Leverage expert know-how through integrated digital service and training processes
- Securing competitiveness through increased efficiency and better capacity utilization of overall systems
Smart Services
- Intelligent ticket system: Optimizes the service process and is used for fast, efficient resolution of error situations on Ersa equipment
- Remote Service: Fast resolution of faults on Ersa equipment through secure remote diagnosis and rapid first aid
- E-learning: Access to digital offerings of process and machine knowledge in the form of interactive training courses
Smart Machine
Application for real-time monitoring of relevant machine and process data with access to machine sensors and other measurement systems.
Associated added values:
- Basis for predictive maintenance
- Increased transparency in production through real-time monitoring
- Reduced downtimes and increased service life of equipment
- Early intervention in the event of deviations, significantly faster response times
- User-oriented live visualization
Smart Production
- Digital machine database
- Live Info: Customer data, general machine information, current configuration (with visual representation), location of the machine
- Documents: Reports from customer acceptance tests (MFU), service reports and instructions, safety documents, waybills/customs documents
- OEE dashboard
- Tracing solution of assemblies and product carriers in connection with manual workstations, peripherals, inspection solutions and Kurtz Ersa equipment for 100% process traceability